What is Offset Printing?
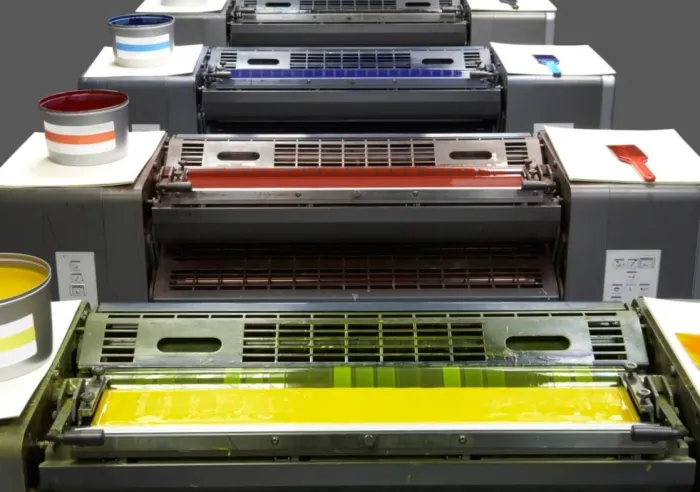
estimated reading time: 6 minutes
Offset Printing, also known as Offset Lithography or Litho-Offset
Printing, was invented over a century ago. Yet it is still the most widely used
commercial printing method in the world today. Known for its speed of operation
and consistently high quality, the offset printing method is the economical
choice for medium to long production runs.
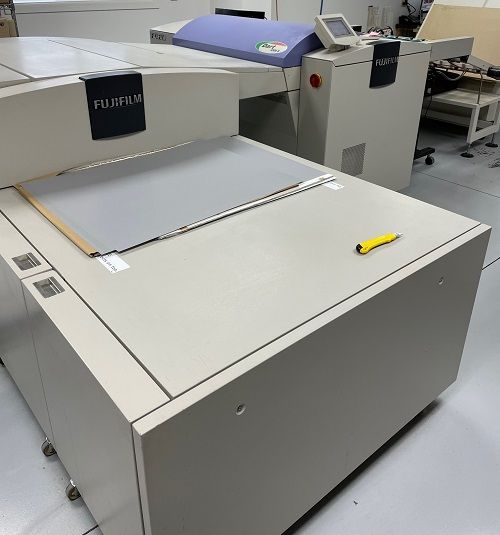
Offset Printing Plates
Printing Plates are a fundamental component of the offset printing process. Custom
made for each project, printing plates are thin sheets of metal (usually aluminum) or polyester
that are etched with the images to be printed. Larger offset presses generally
use aluminum plates because they are more durable.
Each ink color used on an offset project will have its own
printing plate. For example, a one-color project, such as an instruction sheet
printed solely in black ink, will only require one printing plate. Likewise, a
two-color project, such as business letterhead printed with two PMS colors,
will require two printing plates - one plate for each color.
Full-color printing, frequently used for brochures, postcards, and other promotional projects, will require four printing plates: one plate for each of the four CMYK colors of Cyan, Magenta, Yellow, and Black. These four ink colors combine to form full color images. (for a detailed explanation of how the four CMYK ink colors create full color printing, be sure to read our article: What is CMYK?)
Offset printing plates function on the principal that oil
and water do not mix. The image areas on the printing plate are treated to be
receptive to oil-based inks (and thus repel water) and the non-image areas on
the plate are treated to be receptive to water (and thus repel oil-based ink). This
concept will make more sense as you read about the offset printing process
below.
The Offset Printing Process
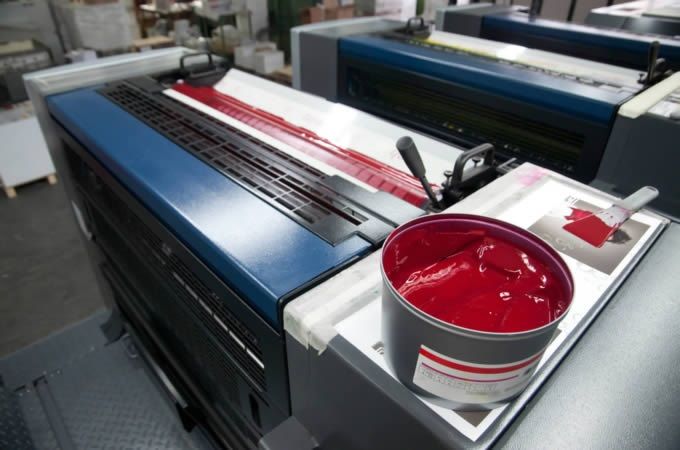
An offset press uses a sequence of spinning rollers.
Depending on their specific function, some of the rollers are referred to as cylinders
or drums. The three primary rollers are known as the plate cylinder, the
blanket cylinder, and the impression cylinder.
Other important rollers include those that distribute the
oil-based inks and others that distribute a water-based dampening solution. There
are additional rollers called feed drums or transferring drums that help move
the paper through the press.
Depending on the press, the roller configuration may vary somewhat but the general function is as follows:
The plate cylinder, which has the printing plate wrapped around
it, contacts the dampening rollers which apply a wetting solution to the plate.
The ink rollers then apply a metered amount of oil-based ink to the plate. This
is where the principal of "oil and water don't mix" comes into play. The ink is
repelled from the moistened non-image areas of the plate. Likewise, the
water-based wetting solution is repelled from the inked image area of the
plate. This maintains the razor sharp detail of the images to be printed.
As the inked plate cylinder rotates, it presses against the rotating blanket cylinder. The blanket cylinder is covered with a synthetic rubber blanket and rotates in the opposite direction of the plate cylinder. As the plate
cylinder and blanket cylinder rotate against each other, the inked image on the
plate transfers to the rubber blanket. Each rotation of the plate cylinder
applies a fresh layer of ink to the blanket.
The next cylinder in the sequence is the impression
cylinder. The impression cylinder rotates in the opposite direction of the
blanket cylinder. The paper (or other substrate to be printed on) travels
between the blanket cylinder and the impression cylinder. The inked image,
which has been transferred to the rubber blanket, is then pressed smoothly onto
the paper as the blanket cylinder and impression cylinders rotate against each
other.
Each ink color has its own set of rollers and cylinders, so
the sequence is repeated for each ink color used on the project. In other words,
the different ink colors are applied in succession as the paper travels through
the press. As you can imagine, all of this automated activity is happening very
fast. Sometimes a protective clear coat
is added after the final ink color has been applied but before the paper exits
the press.
To make sure all the ink colors are printing vividly and in the proper alignment with each other (in register), offset printing presses require a calibration process before starting the actual production run. Known as "make ready", this set-up process involves the printing of multiple test sheets, which are then closely inspected.
Though necessary to ensure a quality outcome, the make-ready
process adds time to the front end of an offset project. However, once an
offset press is set to go and starts running, it prints incredibly fast. As the
press runs, the operator periodically checks a sampling of sheets to ensure a
high level of print quality is being maintained.
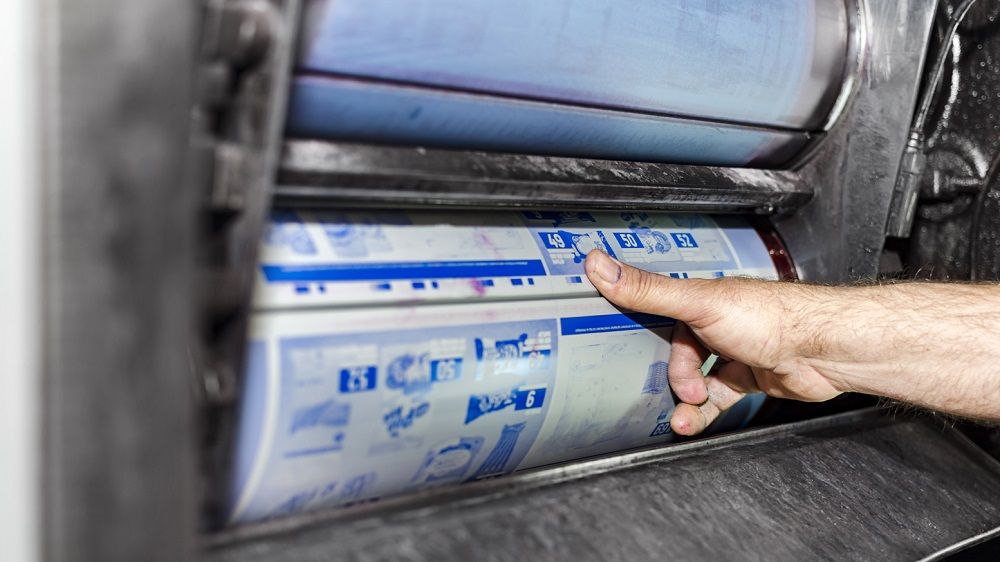
Why is it called Offset Printing?
Offset printing gets its name from the fact that the inked
plate does not contact the paper directly. Instead, the plate cylinder
"offsets" the image onto the rubber blanket, which then applies the inked image
to the paper.
The rubber blanket provides several other important benefits. The rubber reduces wear on the printing plate so that it lasts much longer than
if the plate contacted the paper directly. Plus, the flexibility of the rubber
surface allows it to conform to many different surface textures, thus allowing
a variety of substrates to receive printing that is clean and sharp.
By the way, there are two primary types of offset printing
presses - sheet fed and web.
Sheet Fed Offset Printing
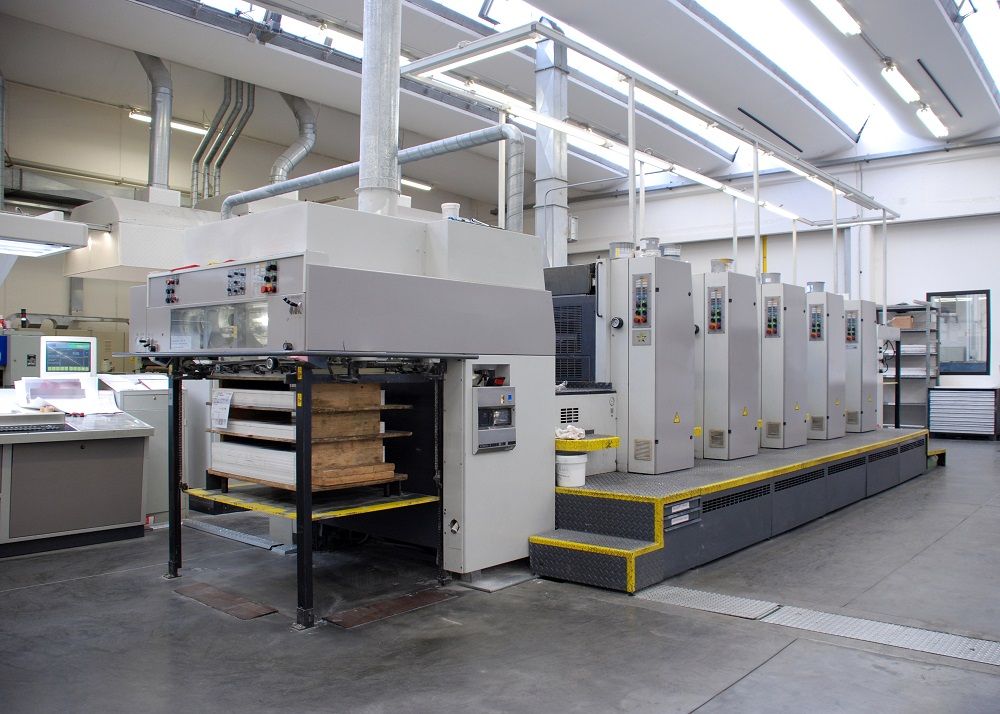
As the name implies, a Sheet Fed Offset Press prints on
individual sheets of paper that are fed into the press one at a time. To ensure
only one sheet is fed into the press at a time, a feeder mechanism uses various
methods, such as suction and friction, to repeatedly separate and feed the
topmost sheet of the paper stack into the press.
These parent sheets are usually quite large so unless the project is a poster, map, or other sizeable document, the sheets are often cut down into multiple sections after being printed.
Sheet fed presses can print on a wide range of paper stocks, including cover weights and cardstocks. The only real restrictions are paper stocks lighter than 50# or thicker than 24pt.
Web Offset Printing
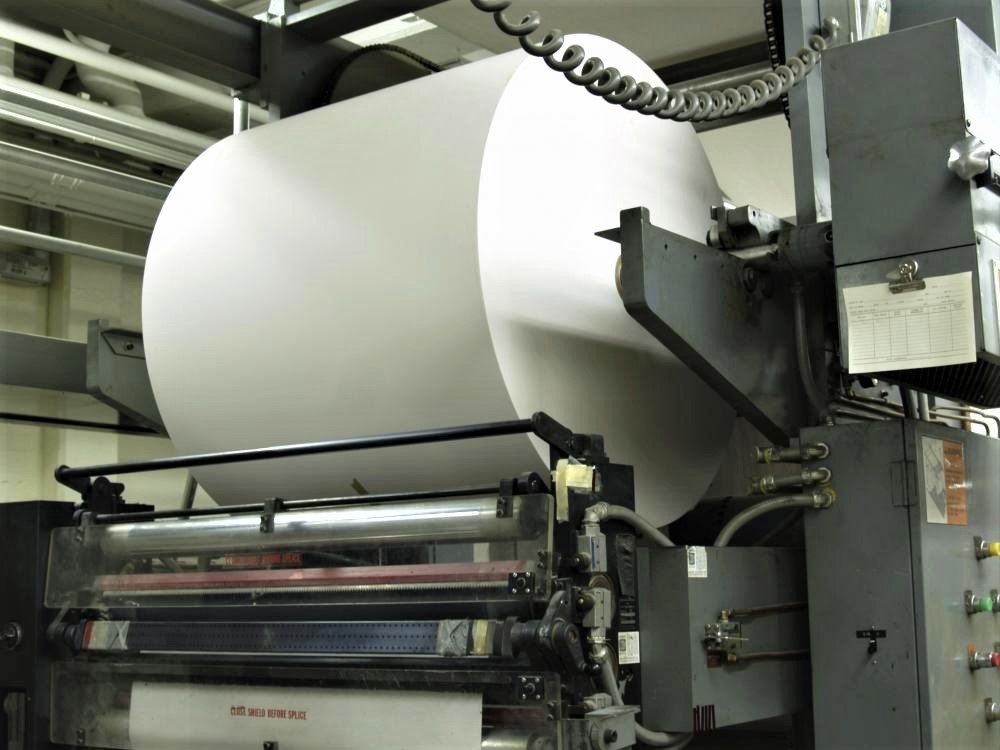
Instead of using individual sheets, a Web Offset Press prints
on paper that is fed from a large continuous roll. The paper moves at a very
high speed using a system of rollers that unwind it from the large roll
and guide it into the press.
The process of moving the paper creates a taught "web" of
paper, hence the name. Also, because the paper is on one continuous roll, it
will need to be cut down into individual pieces after it is printed.
Also known as roll-fed presses, web presses are usually reserved for very large production
runs. Also, a web press does not work well with heavier paper stocks. It is better
suited for light to medium weight paper stocks, with 80# cover generally being the maximum thickness that can run successfully. That said, one of the benefits of a web offset press is that it is ideal for printing on the very thin paper stocks
used for newspapers or the pages of catalogs, magazines, and comic books.
Advantages of Offset Printing
As mentioned above, Offset Printing is the most prevalent
commercial printing process in the world. Here's why…
- Produces consistent colors and high-resolution images
- Lowest cost option for medium and high volume production runs
- Can print CMYK and exact PMS (Pantone) spot ink colors, including metallic inks
- Ideal for projects that require larger sheet sizes or multiple-up printing
- Prints on a wide variety of paper types and thickness
- Compatible with all finishing and bindery options
Looking for Offset Printing Services?
Color Vision has the offset printing capabilities you are
looking for. As an offset printer, we can produce projects using the CMYK
process, one or more PMS colors, or a combination of these two color systems.
We also offer a wide variety of coatings, as well as numerous finishing and bindery choices.
Just give us a call at 800-543-6299 and we'll be happy to discuss your custom printing needs. Or, if you already know your project's specs and want us to email a quote to you, please use our simple Quote Request form.
As always, we look forward to assisting with your next print project!
Related Articles
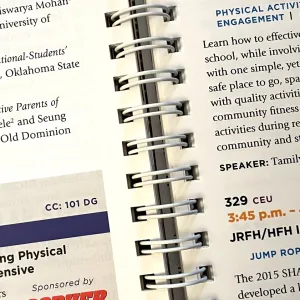
Custom Book Printing: What is Wire-O Binding?
Read This Article
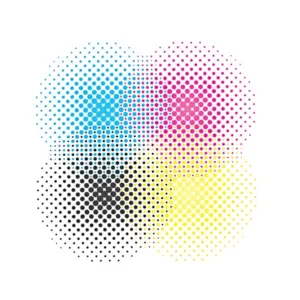
Commercial Printing: What does “Halftone” mean?
Read This Article
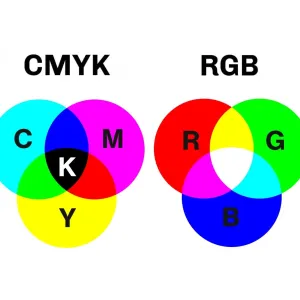
The Difference between CMYK and RGB Color Models
Read This Article

White Space: The Importance of White Space in Graphic Design
Read This Article