Offset Printing: What is Make Ready?
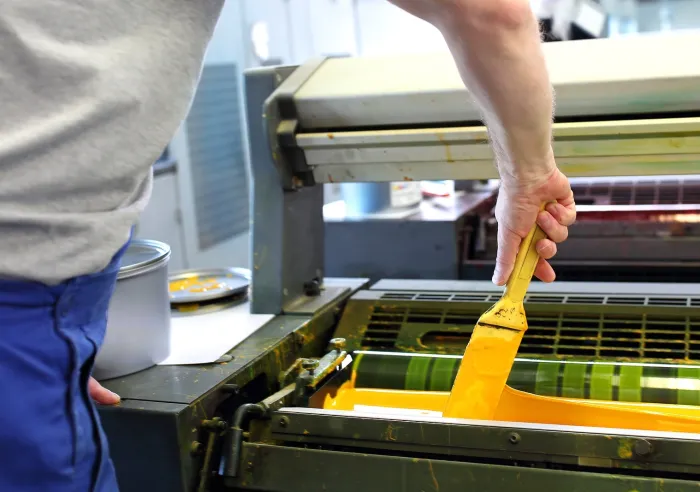
estimated reading time: 5 minutes
What does "Make Ready" mean?
In offset printing, the term "Make Ready" actually has a couple
different meanings depending on the context in which it is used…
1) Make Ready is used as a phrasal verb to describe the initial
set-up and adjustment process needed to prepare an offset printing press for a production
run.
2) Make Ready is also used as a noun to signify the extra
paper needed for printing test sheets while fine-tuning the press settings prior
to the actual production run.
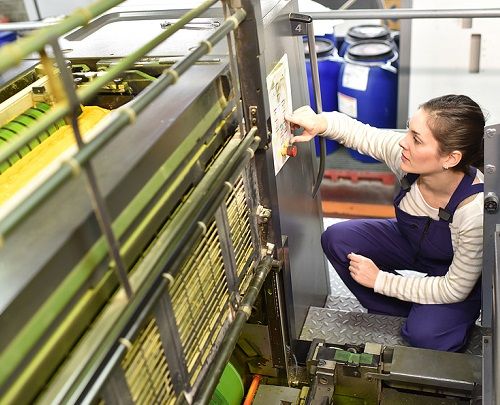
Offset Printing and the "Make Ready" process
Offset printing is the most widely used printing method in
the world. It is known for producing medium to large volumes of print materials
very economically. It is also known for its exceptional print quality.
Offset printing requires the creation of printing plates. Every
ink color used for a particular print project has its own unique printing
plate(s). The plates are aluminum or polyester sheets that have been etched
with the images to be printed.
Offset printing plates function on the principle of oil and
water not being able to mix. As such, the image areas on the plates are treated
to attract oil-based ink while repelling water and the non-image areas on the plates are
treated to attract water while repelling the ink.
When preparing the press for production, each printing plate is formed around a large cylinder within the press. When each plate cylinder rotates, it makes contact with a series of rollers that apply a fresh layer of ink to the plate with each revolution. The plate cylinder also contacts a separate set of rollers that applies a water-based dampening solution to the plate.
The rotating plate cylinder will also press against a counter-rotating
cylinder that has been wrapped in a rubber blanket. The inked image will then offset
from the plate to the rubber blanket. The blanket cylinder will then offset its
inked image to the paper substrate as the paper passes between the blanket
cylinder and a counter-rotating cylinder called the impression cylinder.
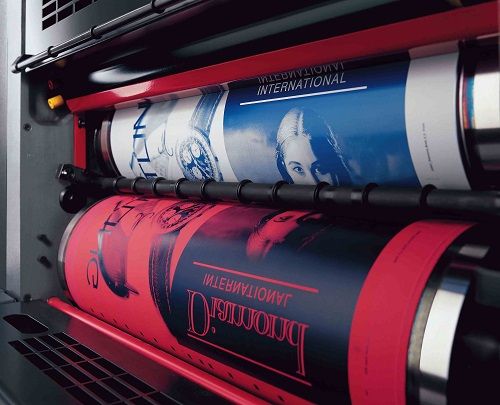
Because an offset printing press involves mechanical motion
and different plates for every production run, each run requires an initial
set-up and adjustment process referred to in the industry as "Make Ready." This
Make-Ready process takes place before any actual printing begins and ensures the
press is properly calibrated for high-quality output.
As you can well imagine, the Make Ready process involves
multiple steps. Hence, it consumes some time at the start of each print run.
However, once the Make-Ready process is complete and the offset press starts
running, the printing speed is lightning fast.
Below are some of the activities Press Operators perform during the Make Ready process…
Inspect Printing Plates - as mentioned earlier, every ink color
used for an offset print project requires its own unique printing plate(s) to
transfer text and images to the printing surface. Prior to mounting the plates,
the press operator checks them for scratches, dings, and other imperfections.
This visual inspection helps to verify the plates are free of any defects that could
negatively affect the quality of the printing.
Mount and Align Printing Plates - after the plates have been
inspected, the cylinders to which they will be mounted are cleaned of any
residual ink or debris. The printing plates are then attached to their
corresponding cylinders. Each plate is aligned evenly across its cylinder
before being secured tightly in place.
Set-Up the Paper Feeding System - once the type, size,
thickness, color, sheen level, grain direction and other paper specifications
have been verified for the project, the paper is loaded into the feed system.
The feed system, or feeder, is a mechanism that smoothly and consistently
guides the paper into the press. Because different jobs use different types of
paper, the feeding mechanism needs to be adjusted for each print run to ensure
it matches the size and type of paper being used for each project.
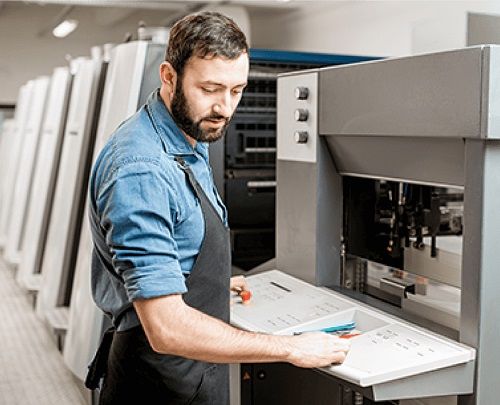
Prepare Inking System - the inks used for offset printing have
a high viscosity. During the make-ready process, the inks for the project are
added to reservoirs known as ink fountains. Each ink color has its own ink
fountain as well as a series of rollers that transfer a steady supply of the
ink to the printing plate. The press operators make the adjustments needed to regulate
the proper flow of ink so that the optimal ink density, consistency, and
coverage will be achieved.
Prepare Dampening System - in addition to ink, a water-based
dampening solution is also transferred to the printing plates via a separate series
of rollers. The press operators control the amount of moisture being applied so
that it flows evenly across the plate. Also, the ink and dampening solution
must achieve the correct balance in order to maintain crisp image quality,
prevent smudging, and ensure proper adhesion to the printing surface.
Run Initial Test Prints - once the plates have been mounted, the inks and
dampening solution have been set up, and all preliminary settings have been
adjusted properly, the next step is to run an initial batch of test sheets
through the press to evaluate the print quality. This is often done at a low
speed.
Adjust Plate Registration - the initial test prints will
show whether or not the ink colors are printing in perfect alignment with each
other. Achieving precise registration often requires fine adjustments to the
lateral and circumferential position of the printing plates. The ink colors must be in strict register for
the printing to appear sharp and well-defined.
Calibrate the Colors - the initial test prints will also
allow the press operator to check the quality of the colors to make sure they
are printing accurately and consistently. Fine tuning the ink and water balance
and/or other settings may be needed to achieve the color density and saturation
required for the production run.
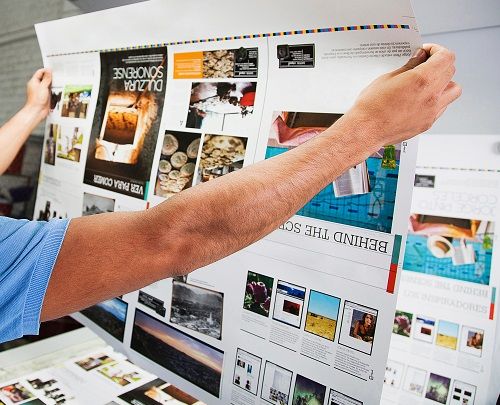
Run Final Set of Test Prints - when all the adjustments have been made, it is time to print the last batch of test sheets. Additional minor tweaks might still be needed, and some can be made while the press is running. Once the test sheets are printing to the desired specifications, the speed of the press is increased and the actual print run begins.
As mentioned at the start of this article, the test sheets
that are printed as part of the make-ready process (before the actual print run
begins) are often referred to as the "Make Ready." Though these sheets serve an important function, they ultimately end up in the recycling bin as waste paper.
Are you looking for Offset Printing Services?
As a full-service commercial printer, Color Vision knows the
Make-Ready process is critical to the success of offset printing jobs. That's
why the experienced press operators at Color Vision Printing perform a thorough
"Make Ready" for every offset project. This optimizes the production run and
ensures our clients will always receive high-quality print materials.
So whether you have a need for books, brochures, catalogs, postcards,
calendars, or any other type of custom printing, give us a call
at 800-543-6299 to discuss your project. Or, use our
simple Quote Request form to send us your specifications and we will email
a quote to you.
Since 1984, Color Vision has been offering
personalized service and affordable print solutions. Whatever your custom printing
needs may be, we look forward to assisting you!
Related Articles
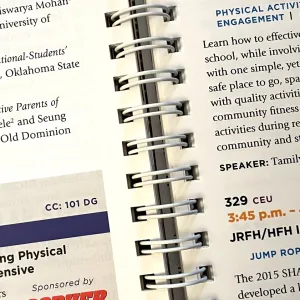
Custom Book Printing: What is Wire-O Binding?
Read This Article
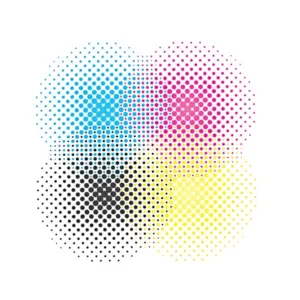
Commercial Printing: What does “Halftone” mean?
Read This Article
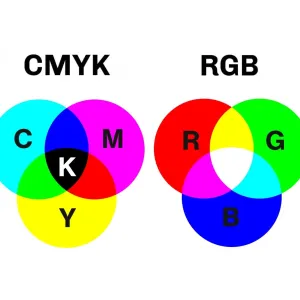
The Difference between CMYK and RGB Color Models
Read This Article

White Space: The Importance of White Space in Graphic Design
Read This Article